ABSTRACT
A new smart concrete aggregate design as a candidate for applications in structural health monitoring (SHM) of critical elements in civil infrastructure is proposed. The cement-based stress/strain sensor was developed by utilizing the stress/strain sensing properties of a magnetic microwire embedded in cement-based composite (MMCC).
This is a contact-less type sensor that measures variations of magnetic properties resulting from stress variations. Sensors made of these mate rials can be designed to satisfy the specific demand for an economic way to monitor concrete infrastructure health. For this purpose, we embedded a thin magnetic microwire in the co re of a cement-based cylinder, which was inserted into the concrete specimen under study as an extra aggregate.
The experimental results show that the embedded MMCC sensor is capable of measuring internal compressive stress around the range of 1–30 MPa. Two stress sensing properties of the embedded sensor under uniaxial compression were studied: the peak amplitude and peak position of magnetic switching field. The sensitivity values for the amplitude and position within the measured range were 5 mV/MPa and 2.5 μs/MPa, respectively.
EXPERIMENTAL SECTION
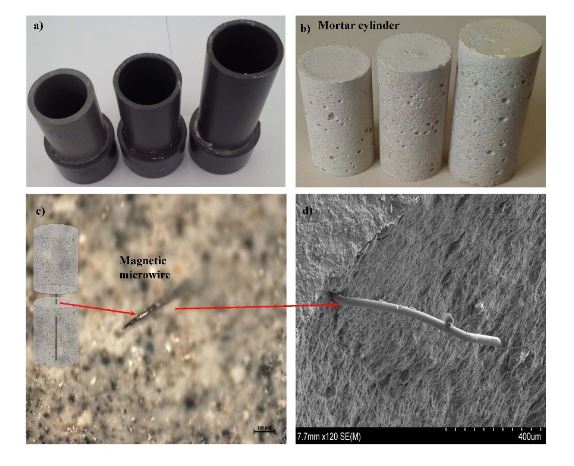
Figure 3. (a) Molds for MMCC sensors; (b) mortar cylinder with an embedded microwire
The magnetic microwire was inserted into the axis of a mortar cylinder. The cylinder geometry was chosen because the calibration of the sensor is simple. The mortar cylinders can be fabricated with different length-to-diameter ratios, as shown in Figure 3a,b. It is worth mentioning that, to maintain the sensing property (bistability) of the highly magnetostrictive microwires, a minimal length of more than a few millimetres is needed. Figure 3c,d shows an embedded magnetic microwire in the transverse plane in the sectioned mortar cylinder.
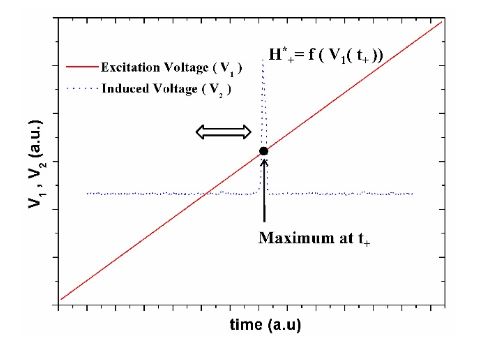
Figure 6. Sharp maximum (blue dot) appears at the end of the pick-up coil when the external field (red line) approaches the switching field
As described above, the pick-up coil is able to detect the motion of a magnetic domain wall represented as an induced voltage peak (see Figure 6) when the external magnetic field caused by the excitation current exceeds the magnetic switching field H*. A voltage peak, maximum or minimum depending on the sense of the excitation magnetic field, is generated when the domain wall starts moving in the sensing pick-up coil.
RESULTS AND DISCUSSION
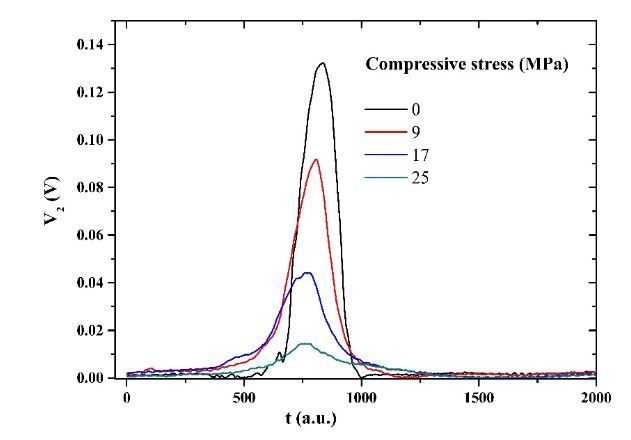
Figure 8. Change of shape (peak amplitude and peak position) of the voltage from the pick-up coil (V2) under applied compressive stress
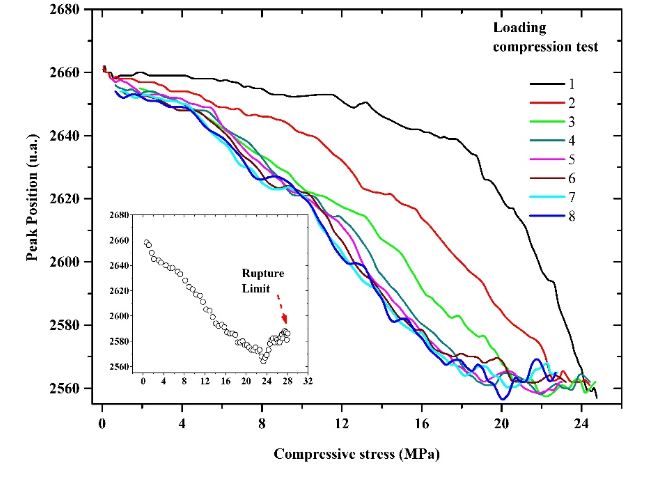
Figure 10. Variation of the peak position of the embedded MMCC sensor
Figure 10 shows that at high applied mechanical compressive stress, the peak position becomes unstable due to the wider half-width of the peak, as shown in Figure 8. Figures 11 and 12 show the means and standard deviations of the sensing properties in the last three cycles, during which the material was considered to be stable.
CONCLUSIONS
A non-destructive testing method for the determination of the mechanical resistance of concrete is presented, consisting of the stress sensitivity of the magnetization reversal of a ferromagnetic microwire. The proposed MMCC sensor was designed to study the possibility of contact-less measurement of compressive stress in a cement-based composite by using an embedded amorphous magnetic microwire.
Two stress sensing properties of the switching field value of the embedded sensor under uniaxial compression were selected: peak amplitude and peak position. The sensitivity values of the amplitude and position within the application range were 5 mV/MPa and 2.5 μs/MPa, respectively. The peak amplitude allows greater precision and measurement range. The MMCC sensor under uniaxial compression shows a precise and repeatable sensing ability for compressive stress.
The experimental results indicate that it is possible to obtain a signal from a microwire embedded in a concrete structure and thus to determine its internal stresses. Hence, it is possible to estimate the structural health of concrete. Their versatility and also its possible integration without physical contact make these sensors suitable and useful for several applications in field of the embedded sensors.
Source: University of Pavol Jozef Safarik
Authors: Jesus Olivera | Margarita González | Jose Vicente Fuente | Rastislav Varga | Arkady Zhukov | Jose Javier Anaya