ABSTRACT
Control systems prototyping is usually constrained by model complexity, embedded system configurations, and interface testing. The proposed control system prototyping of a remotely-operated vehicle (ROV) with a docking hoop (DH) to recover an autonomous underwater vehicle (AUV) named AUVDH using a combination of software tools allows the prototyping process to be unified.
This process provides systematic design from mechanical, hydrodynamics, dynamics modelling, control system design, and simulation to testing in water. As shown in a three-dimensional simulation of an AUVDH model using MATLAB™/Simulink™ during the launch and recovery process, the control simulation of a sliding mode controller is able to control the positions and velocities under the external wave, current, and tether forces. In the water test using the proposed Python-based GUI platform, it shows that the AUVDH is capable to perform station-keeping under the external disturbances.
ROV MODEL
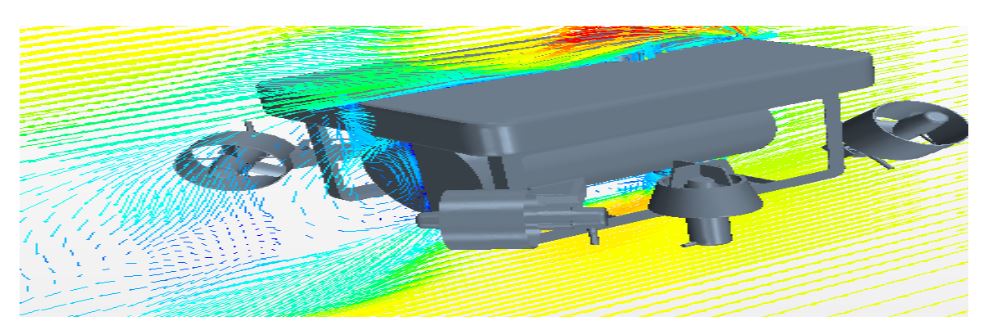
Figure 3. Vector plot at center plane of AUVDH at 0.5 m/s
Figure 3 shows the geometrical model of the ROV. The major components of the ROV such as floater, pod, frame and thrusters, are modelled to ensure the flow characteristic is similar to the actual design. As Figure 3 depicted, the ROV is actuated by six thrusters in six DOFs (namely: surge, sway, heave, roll, pitch, and yaw). The docking hoop for docking the AUV is not included in the model.
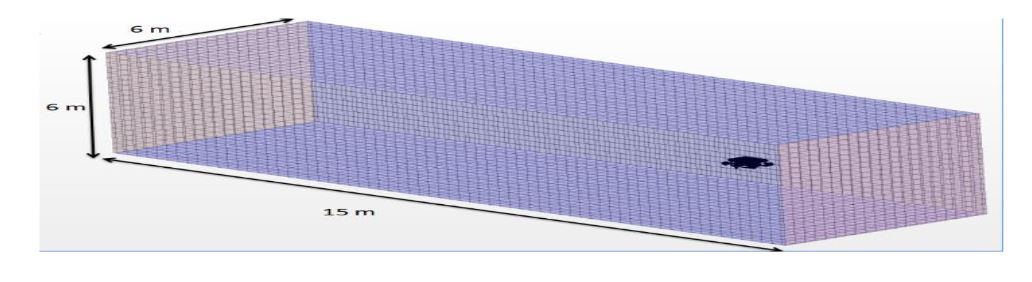
Figure 5. Meshing for flow domain around AUVDH
The flow in fluid domain is expected to be turbulent and isothermal. The fluid properties of water remain unchanged throughout the simulation process. The temperature is fixed at 20 degree Celsius and the water is modelled as an incompressible fluid. It is impractical to set the fluid domain to be infinitely large to analyze damping force acting on ROV in CFD or in towed tank tests. The suggest dimension is around 10 to 20 times larger than the dimension of the ROV (see Figure 5) to ensure the accuracy of the actual flow domain around the ROV.
AUVDH SIMULATION PLATFORM
A total of 10 neurons and one hidden layer are used. The inputs are the X, Y, and Z end point of the tether. While the outputs are the respective force on the body-fixed coordinate of the AUVDH at its CG. As shown in Figure 11, the neural network model (difference in the target and the output) has largely an absolute error of 3.594, and they are also closely correlated in Figure 11. Thus, the neural network model gives a close result to the actual computed values from 3D Catenary BVP.
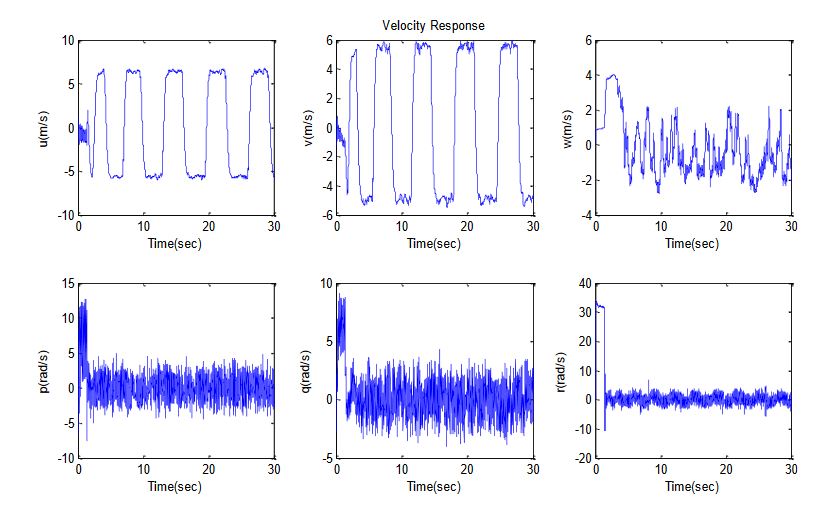
Figure 14. Velocity response
As observed in Figure 14, the position response yields good tracking without excessive discontinuous switching or chattering, as seen in the velocity plots. With the use of the boundary layer around the sliding surface, the chattering has disappeared and results in less oscillatory responses in the velocity. In Figure 13a and 14, the roll and pitch DOF are stable without any control. Further improvement can be performed by tuning the sliding-mode controller gains.
AUVDH GUI TEST PLATFORM
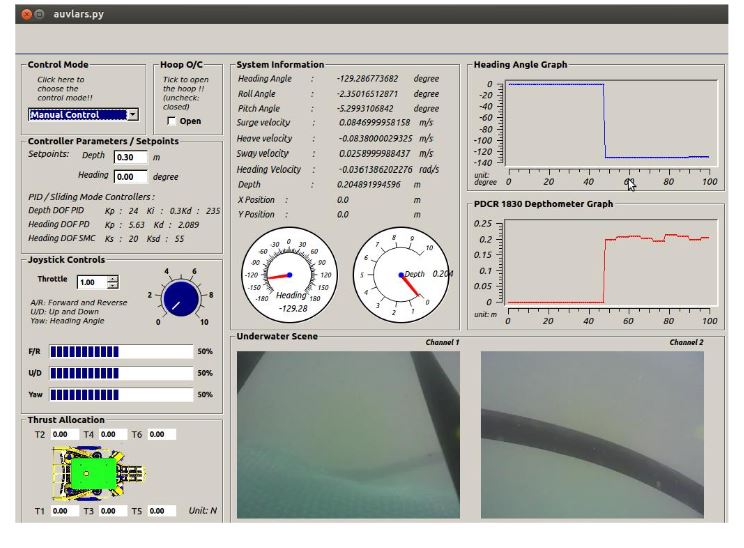
Figure 17. AUVDH GUI control panel layout
A graphical user interface (GUI) is seen as an essential requirement for enhanced operator dexterity. Tele-presence systems have been investigated as a means of realizing highly dexterous and intuitive systems for AUVDH. The AUVDH GUI control system panel consists of two primary functions: send control commands to control the thrusters manually and automatically; and display sensors and thrusters status in real-time. The actual layout of the GUI control panel is shown in Figure 17.
RESULTS AND DISCUSSION
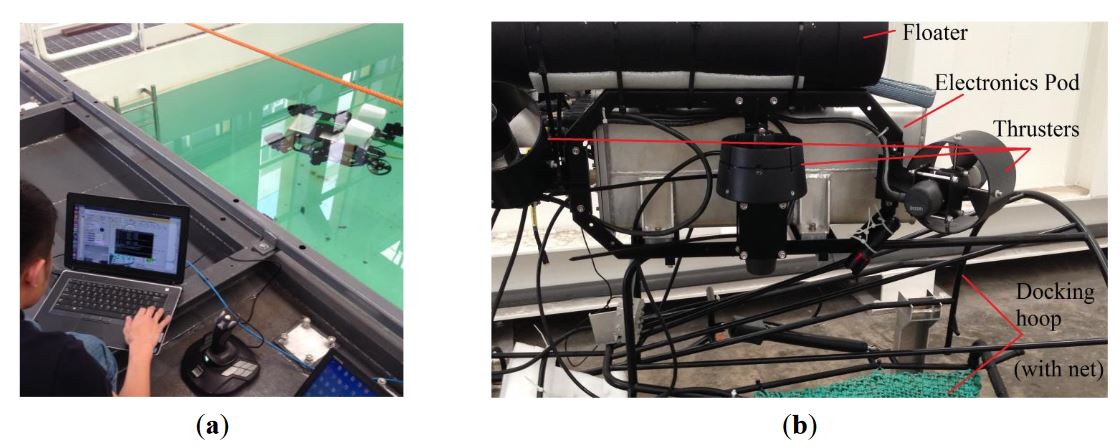
Figure 18. Experimental test setup of AUVDH (a) near water tank (b) on ground after test
The ROV was tested in a water tank as shown in Figure 18 a. A few tests were conducted on the open-loop AUVDH system for sensor fusion and closed loop control. The AUVDH is a tethered and remotely-operated underwater robot as shown in Figure 18b. The AUVDH is powered by a 230VAC power supply. The mass of the vehicle is approximately 135 kg and its dimensions are 1.5 m long × 1 m wide × 1.7 m high. The exterior components consist of a docking hoop to dock the AUV, six thrusters, DVL, altimeter, IMU, floater, and aluminium casing to house the electronics.
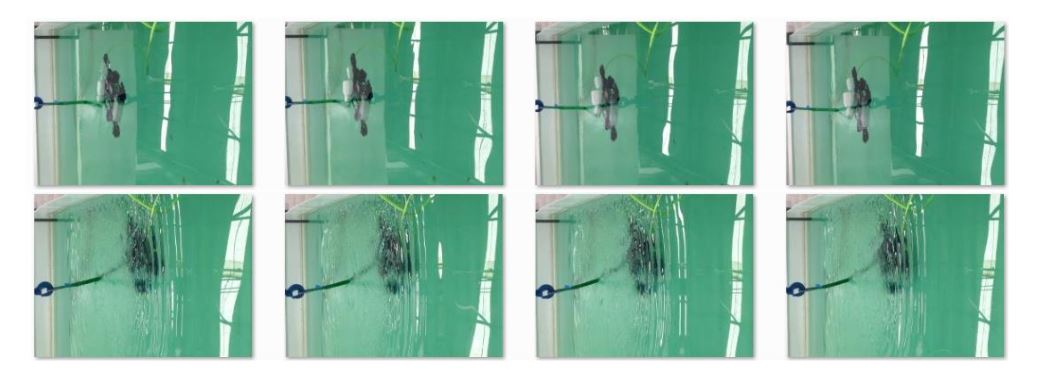
Figure 19. Experimental test image (yaw then heave) during test in water tank
Few trials in the commanded heave and yaw directions were conducted, as seen in the test images shown in Figure 19. During the experiments, the performance of the open-loop guidance and closed-loop control systems using the sliding-mode controller were fully assessed.
CONCLUSIONS
This paper has reported a preliminary experimental evaluation of a model-based sliding-mode controller for a low-speed manoeuvring of an actuated remotely-operated vehicle (ROV) named AUV docking hoop (AUVDH). We considered the simple case of an AUVDH plant dynamics model employing constant added mass, buoyancy, linear and quadratic drag, and thrust input. Dynamic modelling and simulation of AUVDH during launch and recovery of the AUV were performed. The tether model was modelled using the back propagation neural network.
The control strategy from launch to recovery in 2D and 3D was simulated using MATLAB™ and Simulink™ prior to actual implementation. The control simulation using a sliding mode controller (SMC) was proposed to control the surge, sway, heave, and yaw positions and velocities of the AUVDH under the sea wave, current and tether forces. In summary, the proposed SMC scheme is able to control the AUVDH during launch and recovery of the AUV under the external disturbances.
The experiment tests conducted in water tank shown that the SMC is able to control the depth and yaw position of the AUVDH with small roll and pitch angles. However, the experiments do not demonstrate the effects of variations in controller gains or change due to the thruster configuration matrix and inertia matrix for the closed-hoop condition. The identification and closed-loop comparison with other controllers needs to be performed. We hope to report an experimental evaluation of these conditions on the performance of these controllers in the sea trial.
Source: Newcastle University
Authors: Wei Peng Lin | Cheng Siong Chin | Leonard Chin Wai Looi | Jun Jie Lim | Elvin Min Ee Teh
>> 200+ Matlab Projects for Control System for Engineering Students
>> 80+ Matlab Projects based on Power Electronics for Engineering Students
>> More Matlab Projects on Embedded Systems for Engineering Students