ABSTRACT
This work presents a simulation framework developed under the widely used Robot Operating System (ROS) to enable the validation of robotics systems and gas sensing algorithms under realistic environments. The framework is rooted in the principles of computational fluid dynamics and filament dispersion theory, modeling wind flow and gas dispersion in 3D real-world scenarios (i.e., accounting for walls, furniture, etc.).
Moreover, it integrates the simulation of different environmental sensors, such as metal oxide gas sensors, photo ionization detectors, or anemometers. We illustrate the potential and applicability of the proposed tool by presenting a simulation case in a complex and realistic office-like environment where gas leaks of different chemicals occur simultaneously.
Furthermore, we accomplish quantitative and qualitative validation by comparing our simulated results against real-world data recorded inside a wind tunnel where methane was released under different wind flow profiles. Based on these results, we conclude that our simulation framework can provide a good approximation to real world measurements when advective airflows are present in the environment.
RELATED WORK
Gas dispersion simulation (GDS for short) is a task that has been persistently addressed by different disciplines such as meteorology and computer science. Several taxonomies have been reported to classify the different approaches, for example, according to the spatial scale (i.e., macro and micro models), or to the nature of the dispersion model. According to the latter taxonomy, simplistic GDS models can be classified as box, Gaussian and analytical models. These models make strong assumptions regarding the underlying spatio-temporal properties of the gas distribution.
STRUCTURE OF THE SIMULATOR
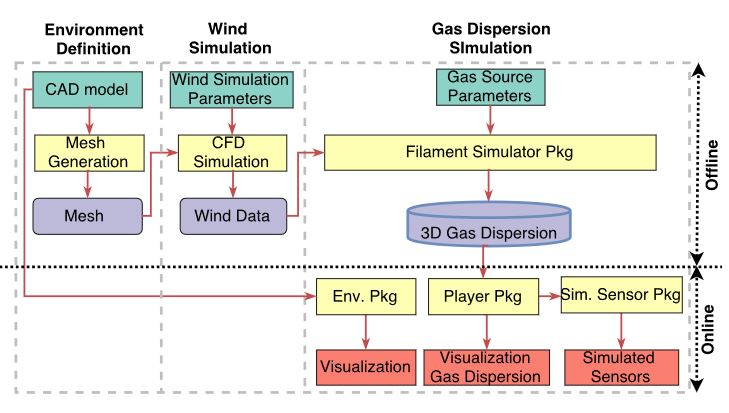
Figure 1. Block diagram of the presented gas dispersion simulator. Green, blue and red blocks represent input, intermediate and output data, respectively, while yellow blocks are processes
The presented simulator follows a three-stages structure as depicted in Figure 1. In the first stage, the environment is defined by specifying the dimensions, obstacles and physical wind inlets/outlets among other parameters. Then, by means of CFD tools, the wind flow patterns within the environment are simulated, and finally, in the last stage, the estimation of the gas dispersion is computed by applying the filament dispersion model.
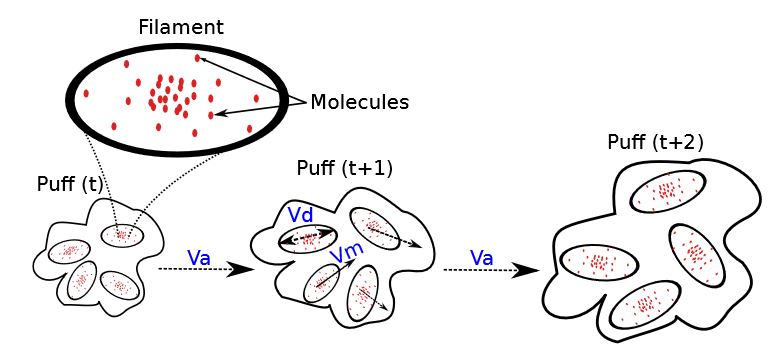
Figure 4. A gas release is modeled as a sequence of puffs, each one composed of multiple filaments (being a filament a 3D Normal distribution of gas molecules)
The filament dispersion model states that a chemical release can be represented as a sequence of puffs, each one composed of n filaments, and each filament being modeled as a 3D Normal distribution of molecules (see Figure 4). The puffs are manipulated by turbulent and molecular diffusion, while, at the same time, are being transported advectively by wind.
IMPLEMENTATION: THE ROS-PKG
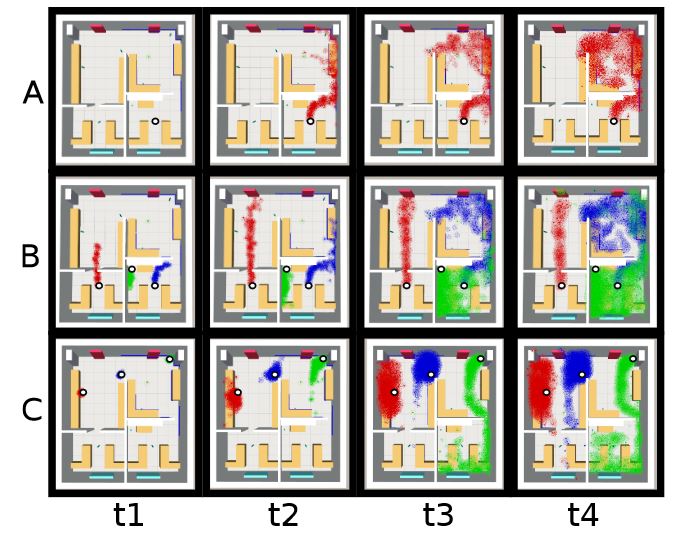
Figure 6. Snapshots of the gas dispersion at four time-steps
Since this package has basically no computational burden, it can run online, being only limited by the size of the environment and the desired refresh rate. Moreover, it facilitates loading multiple gas concentration gridmaps simultaneously, enabling the consideration of multiple gas sources and different chemical species. Figure 6 shows different gas dispersion simulations for the multi-room environment, varying the wind conditions, the gas source location, or the number and type of chemicals released.
VALIDATION
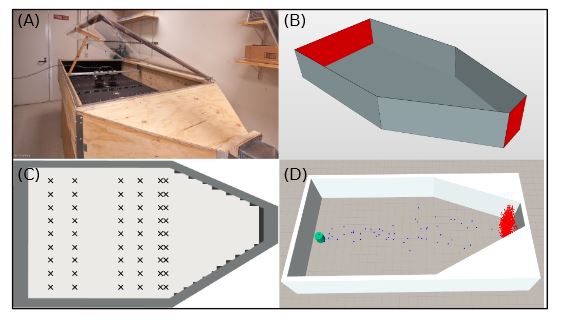
Figure 7. The wind tunnel test-bed facility: (A) picture of the physical wind tunnel used to collect the dataset
The simulation parameters are thus selected in order to follow the actual experimental setup as close as possible. For example, the concentration level at the gas source location is used to determine the number of filaments in the simulation. Figure 7 shows a picture of the wind tunnel, the respective CAD model used during simulation, a detailed view of the e-nose locations within the environment, and a snapshot of a simulated gas plume.
CONCLUSIONS
In this work, we present GADEN, a gas dispersion simulator that is aimed at robotics applications. GADEN is a modular tool developed in ROS that allows for creating sophisticated simulations that can be used used to validate, for example, Mobile Robotics Olfaction (MRO) algorithms. While several gas dispersion simulation engines exist, GADEN provides several improvements over the state-of-the-art. First, GADEN is fully developed in ROS, which allows for integrating robotics algorithms into the simulation engine.
In this way, gas sensing and robotics algorithms, such as navigation and 3D perception, can be integrated and validated concurrently. Second, GADEN provides an integrated solution to import sophisticated 3D-CAD models of the environment. In comparison, existing simulation tools allow for defining geometrical models from the environment, but only as simplistic models, where only a few cube-like obstacles might be present. Third, GADEN allows for simulating environments where multiple gas sources of different analytes can be present simultaneously.
This is particularly useful to validate algorithms for gas discrimination and the mapping of different chemical compounds. Fourth, GADEN’s dual architecture, namely, the online and offline components, allow for easing off the computational demands of gas dispersion simulation. Existing simulation engines, on the other hand, compute gas dispersion as the simulator is being executed. The drawback of this approach is that, as the simulation time progresses, the computational demands increase substantially, limiting, in this way, the usability of the simulator.
In order to perform a quantitative evaluation of GADEN, we used real-world data acquired inside a wind tunnel, where a single emitting ethanol gas source was placed and an array of MOX sensors collected measurements. We thus created a CAD model of the wind tunnel and performed simulations under different airflow conditions. We compared the real-world measurements against simulated measurements at the sensor’s positions using the symmetric Kullback–Leibler divergence (sKLD).
Our comparison shows a high degree of similarity between simulated and actual measurements when an advective airflow is present. When gas dispersion is dominated by turbulence, simulated and real-world measurements show higher divergence. This result is expected due to the the stochastic nature of turbulence, which is not considered in the gas dispersion simulation approach presented in this work.
Source: University De Malaga
Authors: Javier Monroy | Victor Hernandez-Bennetts | Han Fan | Achim Lilienthal | Javier Gonzalez-Jimenez