ABSTRACT
One of the crucial actions to be performed during a grasping task is to avoid slippage. The human hand can rapidly correct applied forces and prevent a grasped object from falling, thanks to its advanced tactile sensing. The same capability is hard to reproduce in artificial systems, such as robotic or prosthetic hands, where sensory motor coordination for force and slippage control is very limited.
In this paper, a novel algorithm for slippage detection is presented. Based on fast, easy-to-perform processing, the proposed algorithm generates an ON/OFF signal relating to the presence/absence of slippage. The method can be applied either on the raw output of a force sensor or to its calibrated force signal, and yields comparable results if applied to both normal or tangential components. A biomimetic fingertip that integrates piezoresistive MEMS sensors was employed for evaluating the method performance.
Each sensor had four units, thus providing 16 mono-axial signals for the analysis. A mechatronic platform was used to produce relative movement between the finger and the test surfaces (tactile stimuli). Three surfaces with submillimetric periods were adopted for the method evaluation, and 10 experimental trials were performed per each surface. Results are illustrated in terms of slippage events detection and of latency between the slippage itself and its onset.
SLIPPAGE DETECTION PROCEDURE

Figure 1. Block scheme of the slippage detection method
The proposed method consists of three main blocks in cascade between the input signal, which is the raw voltage output of the employed force sensor, and the ON/OFF output, which is the final slippage signal. Figure 1 shows the blocks. Although the calibrated force information is not used as input, it should be noticed that the algorithm output somehow depends from the applied pressure level, i.e., the higher the exerted pressure on the sensor is, the higher the amplitude of the signal available for the ON/OFF signal generation is. However, the applied pressure is directly proportional to the raw voltage, allowing to exploit the latter without loss of information.
EXPERIMENTAL SETUP, PROTOCOL AND ALGORITHM IMPLEMENTATION
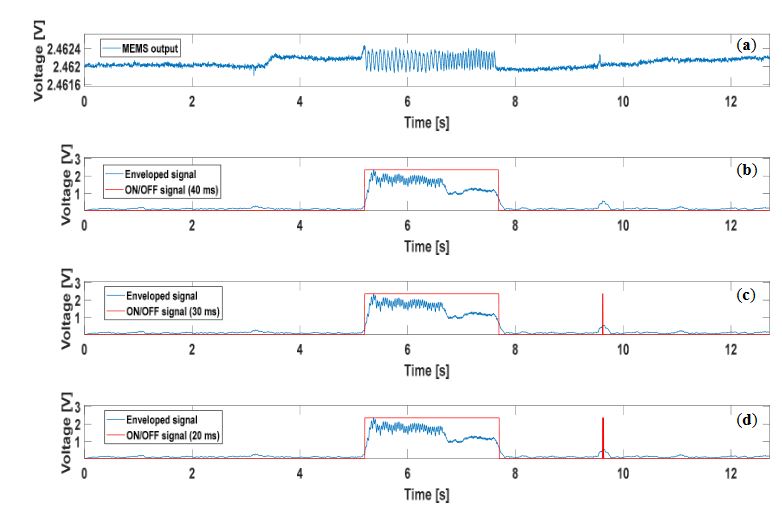
Figure 4. (a) Voltage output from one of the 16 tactile units; (b) result of the algorithm application
Figure 4 illustrates the output from one of the tactile units during a trial, and the result of the algorithm (ON/OFF signal) calculated with different time windows. The enveloped signal is considered to be ON if its average value within the time window overcomes an empirically established threshold. The threshold can be adjusted according to the employed sensor technology; it may vary from a kind of sensor to the other. In this case, it was set to 0.5 V.
EXPERIMENTAL RESULTS
First, it is crucial to evaluate the delay D between the beginning of the platform movement with respect to the biomimetic finger, and the OFF to ON transition of the slip signal. The time instant tst at which the platform starts moving was computed as follows.
CONCLUSIONS AND FUTURE WORK
In this paper, a novel method for detection of slippage events was proposed. Said method was presented through a detailed description of its sub-blocks, which include simple operations such as digital filtering, rectification and envelope of the input signal. Such sub-blocks are cascaded to generate the ON/OFF slippage identification signals. The method was accurately validated on piezoresistive MEMS sensors; an ad hoc automated setup was experimented for this purpose.
A total of four sensors, integrated into a biomimetic fingertip, were employed; each sensor featured four channels, leading thus to sixteen channels for the slippage detection analysis. Relative movements lower than 5 μm between the sensor and the contact surface were detectable through the developed algorithm.
True positives were detected in 100% of the cases and minimum average delays resulted lower than 50 ms. False positives have been detected in no more than 1.01% of the cases. Remarkably, it is not necessary to employ the force value to apply the method: the raw voltages of sensor outputs (relating to the force) can be used as input. In this manner the force estimation and the ON/OFF slip signal generation can be performed as parallel operations rather than consecutive.
Source: University Campus Bio-Medico Di Roma
Authors: Rocco A. Romeo | Calogero M. Oddo | Maria Chiara Carrozza | Eugenio Guglielmelli | Loredana Zollo
>> More Matlab Engineering Projects for Beginners